In der Industrie sind Koordinatenmessmaschinen oder 3D-Koordinatenmessmaschinen wichtige Werkzeuge in der Produktion und der Qualitätskontrolle. Die Technik ermöglicht eine genaue Messung von Bauteilen in drei Dimensionen. Ihnen kommt in der modernen Fertigung eine hohe Bedeutung zu.
Was definiert eine Koordinatenmessmaschine? Eine Koordinatenmessmaschine bzw. eine 3D-Koordinatenmessmaschine ist ein Messinstrument, das in der modernen Industrie genutzt wird, um die geometrischen Eigenschaften von Bauteilen zu ermitteln. Diese Maschinen gibt es in vielen verschiedenen Ausführungen, mit unterschiedlichen Messverfahren. Die Messung erfolgt durch den Gebrauch von Sensoren, die ein kartesisches Koordinatensystem nutzen, um die Position von Objektoberflächen genau zu bestimmen.
In unserem Hause Q-Tech verwenden wir Koordinatenmessmaschinen der Marke ZEISS. Welche das sind, erfahren Sie hier in diesem Artikel. Wenn Sie mehr zu den technischen Daten der einzelnen Maschinen wissen wollen, werfen Sie am besten einen Blick auf unser Equipment.
Funktionsweise
Eine Koordinatenmessmaschine besteht aus drei Hauptkomponenten:
- Dem Messkopf
- Einem mechanischen Aufbau (Portal, Ständer mit Horizontalarm etc.)
- Einer Software für die Datenaufzeichnung und -analyse
Der Messkopf fährt an den Achsen der Maschine entlang und sammelt währenddessen Daten von der Oberfläche des Bauteils. Diese Daten werden von der Software erfasst und analysiert. Anschließend kann der Prüfer die Abweichungen von der Soll-Geometrie des Bauteils bestimmen.
Als Basis für 3D-Koordinatenmessmaschinen dient häufig eine CNC-Steuerung. Dadurch kann der Verfahrweg des Messkopfes genau programmiert werden, damit die einzelnen Punkte in dem Koordinatensystem exakt definiert sind.
Dieses Verfahren zählt mit zu der Längenmesstechnik. Dabei ist jede Verfahr-Achse (X, Y und Z) jeweils mindestens einem Längenmesssystem zugeordnet.
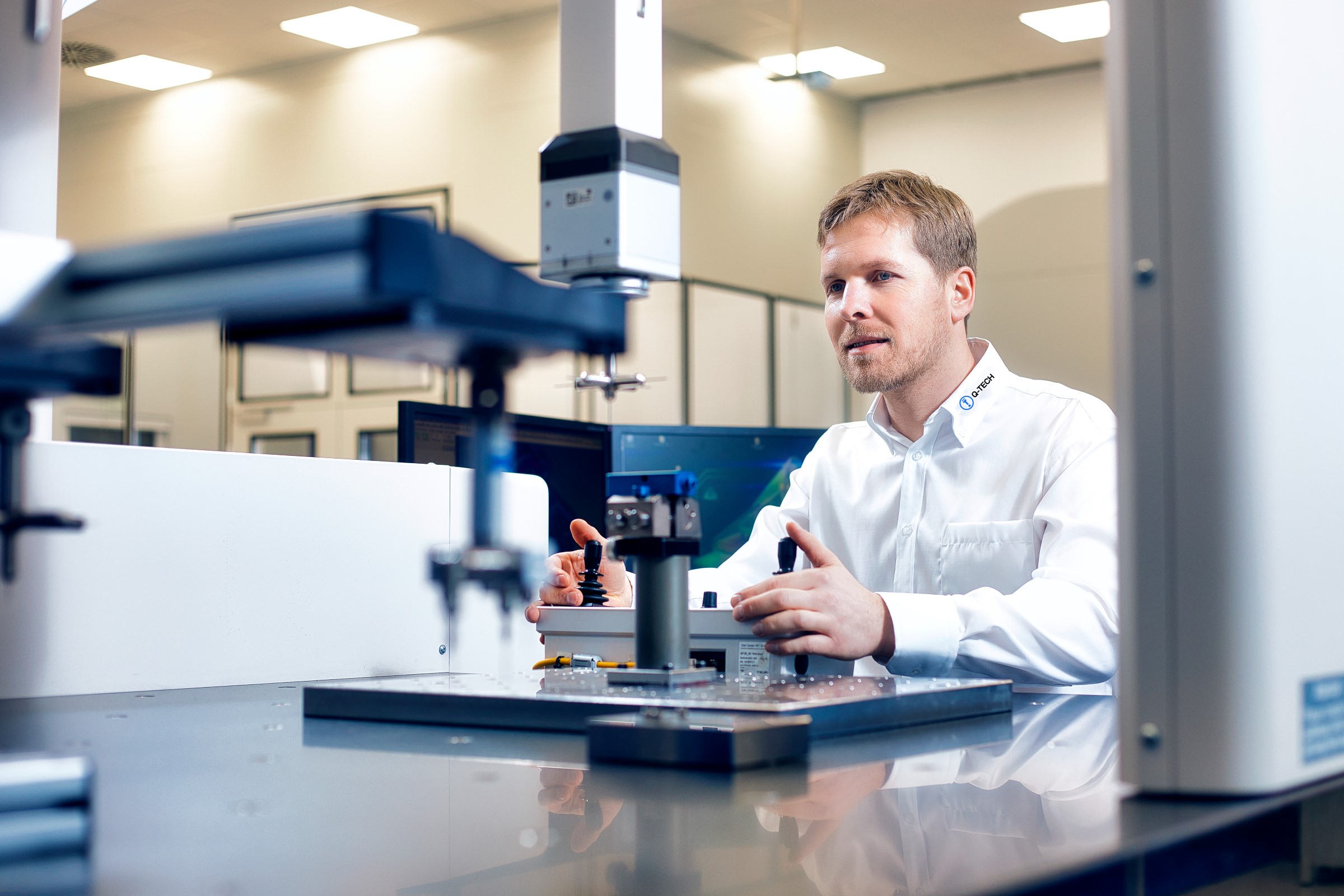
Grundbauarten
In dem Bereich der Koordinatenmesssysteme gibt es verschiedene Bauweisen und Grundbauarten, um die drei rechtwinkligen Führungen X, Y und Z zu realisieren.
- Ständerbauweise: Bei diesem Koordinatenmesssystem ist die Pinole mit dem Messkopfsystem horizontal beweglich. Diese können entlang eines Ständers in vertikaler Richtung bewegt werden. Die zweite horizontale Bewegung erfolgt meist durch ein Verfahren des Ständers entlang der Messplatte oder mithilfe eines beweglichen Tisches.
- Brückenbauweise: Hier sind die beweglichen Achsen und der Aufspannbereich voneinander getrennt. Das ermöglicht einen großen Messbereich und somit das Erfassen von sehr großen Werkstücken. Maschinen mit der Brückenbauweise kommen häufig im Flugzeugbau zum Einsatz.
- Portalbauweise: Die tragende Pinole des Messkopfsystems sitzt an dem Portal-Querbalken. Diese Pinole ist in horizontaler Richtung entlang des Portal-Querbalkens beweglich. Die Lagerung des Portals erfolgt mit zwei Füßen an den Rändern des Gerätetisches. Gleichzeitig ist das Portal in horizontaler Richtung entlang des Gerätetisches beweglich. Portalmessmaschinen auf Koordinatensystem-Basis bieten geringe Messabweichungen, eine gute Zugänglichkeit und einen Messbereich, der ausreichend groß ist. Heutzutage gelten sie als die beliebteste und meistgenutzte Bauweise.
- Auslegerbauweise: Als Basis dieser Bauweise dient ein Auslegearm, der an dem Messkopfsystem befestigt und in vertikaler Richtung beweglich ist. Darüber hinaus sind zwei weitere Achsen jeweils senkrecht zueinander in horizontaler Richtung bewegbar. Die horizontale Bewegung kann entweder durch einen beweglichen Tisch oder bei einer feststehenden Tischvariante durch bewegliche Aufbauelemente des Auslegers erfolgen.
Diese Grundbauarten unterliegen der technischen Norm DIN EN ISO 10360-1:2003. Hersteller haben sich während der Produktion dieser Maschinen an diese Vorgaben zu halten.
Sensoren
Die Messung bei Koordinatenmessmaschinen kann entweder taktil oder optisch erfolgen. Bis in die 90er-Jahre waren taktile Sensoren der Vorreiter in der Messtechnik. Mittlerweile werden vermehrt auch optische Verfahren eingesetzt.
Der Grund ist, dass in den letzten Jahrzehnten die Anforderungen gestiegen sind und so die technischen Bauteile immer bessere Sensortechnik erfordern.
Um die Flexibilität von Koordinatenmesssystemen zu verbessern, werden heute auch mehrere Sensor-Methoden miteinander kombiniert. Überdies ist es bei den meisten Systemen möglich, den Sensor bzw. Taster auszutauschen, um mehrere komplexe Messaufgaben mit einer einzelnen Maschine zu lösen.
Mechanische/Taktile Antastung
Die Antastung der Werkstückoberfläche erfolgt mit einem Messtaster. Die Messaufgabe bestimmt überwiegend die unterschiedlichen geometrischen Formen des Tastelements. Häufig werden Kugeln mit Materialien aus Industrierubin, Hartmetall oder Siliziumnitrid genutzt. Der menschliche Tastsinn dient für den Vorgang als Orientierung.
Bei der Antastung wirkt eine Messkraft von rund 0,01 bis 0,2 N. Aus diesem Grund verbiegt sich der Taststift. Diese “Verbiegung” muss in der Messung berücksichtigt werden. Daher erfolgt automatisch eine Korrektur des Tasters.
Berührungslose Antastung
Zur berührungslosen Antastung zählen optische, elektrische und röntgentomografische Sensoren.
Genau betrachtet, kann jeder elektrische oder optische Sensor in Koordinatenmesssystemen eingesetzt werden, um den Messbereich mithilfe des X-Y-Z Positioniersystems zu vergrößern.
Zu der berührungslosen Antastung zählen:
- Triangulationssensoren (Liniensensoren, Fotogrammetrie, Streifenprojektion)
- Bildverarbeitungssensoren (Kantenfinder, Binär-Verarbeitung)
- Interferometer (Laserinterferometer, Weißlichtinterferometer)
- Tunnelstromsensoren
- Röntgenröhrenstrahlung und Detektoren
Vorteile
3D-Koordinatenmessmaschinen sind mittlerweile seit mehreren Jahren der Industriestandard in der Qualitätssicherung von Bauteilen.
Hier sind einmal die Vorteile der Maschinen in ihrer Gesamtheit zusammengefasst:
- Hohe Präzision
- Bieten eine hohe Wiederholgenauigkeit
- Erfassung von komplexen Geometrien
- Messdaten lassen sich automatisch erfassen
- Menschliche Fehlerquellen werden reduziert
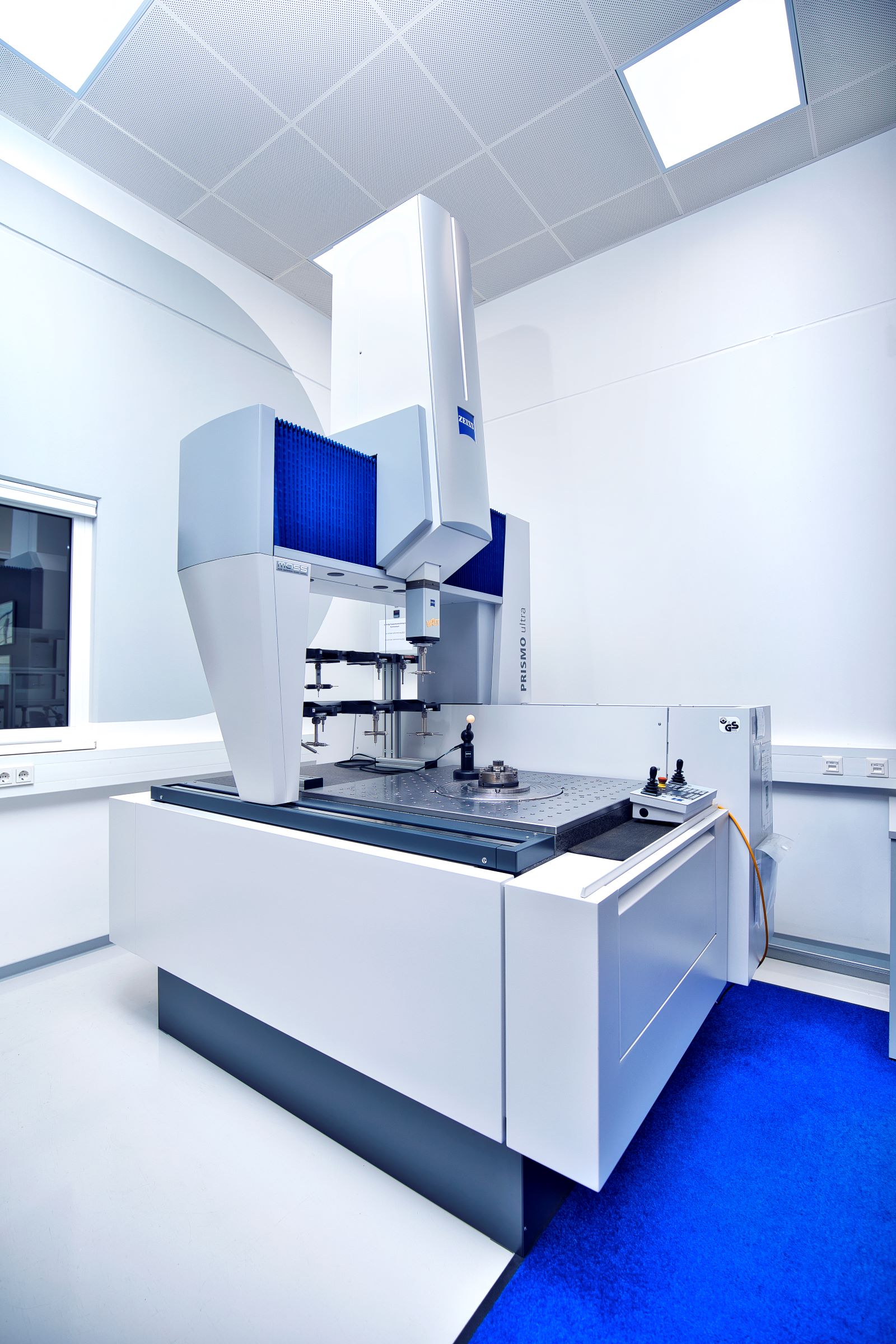
Bedeutung der Maschinen in der Industrie
Wie bereits erwähnt, spielen Koordinatenmessmaschinen eine wichtige Rolle bei der Qualitätssicherung in der Fertigung. Sie ermöglichen es, die Maßhaltigkeit von Bauteilen zu überprüfen.
Darüber hinaus erhöhen Koordinatenmessmaschinen aber auch die Effizienz in der Produktion, weil die Hersteller der Bauteile in relativ kurzer Zeit die Qualität ihrer Produkte bestimmen und gegebenenfalls Anpassungen in Echtzeit vornehmen können.
Einsatzbereich
Grundsätzlich gesehen, sind Koordinatenmessmaschinen universell einsetzbar.
Dabei eignen sie sich hervorragend für die statistische Prozesssteuerung oder für eine 100-% Kontrolle in kleinen Serien.
Zu den Anwendungsbereichen zählen geschweißte oder gegossene Bauteile oder auch ganze Baugruppen wie z. B. Motorblöcke, Karosserien, Gehäuse oder Verzahnungen.
Häufige Branchen sind die Automobilindustrie, der Luftfahrzeugbau und bei modernen 3D-Koordinatenmessmaschinen die Medizintechnik. Die Messmaschinen werden aber auch in vielen anderen Bereichen der Industrie eingesetzt.
Die Koordinatenmessmaschinen bei Q-Tech
Als Experte auf dem Gebiet der Messtechnik bietet Ihnen Q-Tech eine ganze Reihe an Messdienstleistungen an, die auf Ihre spezifischen Bedürfnisse zugeschnitten sind.
In unserem Hause setzen wir auf die Koordinatenmessmaschinen des Herstellers ZEISS.
In unserem Repertoire befinden sich eine ZEISS PRISMO ULTRA, eine ZEISS PRISMO VERITY, eine ZEISS ACCURA 7, eine ZEISS ACCURA und sogar eine ZEISS O-INSPECT 863, die sowohl die optische als auch die taktile Messtechnologie in sich vereint.
Unsere Koordinatenmessmaschinen bieten Ihnen höchste Messgenauigkeit und einen möglichst schnellen Messvorgang.
Fazit
Koordinatenmessmaschinen zählen zu den wichtigsten Werkzeugen in der modernen Fertigung und der Qualitätskontrolle. Sie ermöglichen den Bauteilherstellern, die Maßhaltigkeit ihrer Produkte einzuhalten und somit die Kundenzufriedenheit und Effizienz zu gewährleisten.
Kontaktieren Sie uns und kommen Sie in den Genuss unserer präzisen Messdienstleistungen, damit wir einen entscheidenden Beitrag zur Optimierung Ihrer Fertigungsprozesse leisten können.